FORM-FINDING STRATEGIES | ENHANCING ROBOTIC FUNCTION
Over the past 15 years, researchers in architecture and construction have been exploring the possibilities
of employing industrial robotics to help create new kinds of architectural forms. There is now a wealth of
research in this area, which manufacturers can draw upon to inform new robotic processes, due to the power
that they entail in the direct path from digital design to fabrication. For architects, designers and
construction managers, this research also points the way to new design possibilities.
In the scope of this training material, examples from current architectural and design research are
explored. Recent publications from ROBArch, CuminCAD and prominent universities were analysed to identify
key hardware requirements. The key findings of the literature review show that custom end effectors, direct
human interaction with technology and vision embedded systems are necessary to correspond to the needs of
manufacturing bespoke designs. The results of this research hints that there is a need for a paradigm shift
in the way fabrication is thought, as the design methods used in the early exploratory stages directly
correlates with the way the industrial robots function and manufacture.
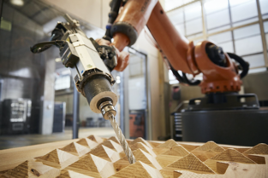
End-Effectors
IRAs respond to numerous tasks by utilising different end effectors (EEs) by tools. EEs are gateways to
manipulate various materials as well as exploring numerous ways of systems of thinking. The possibility of
attaching any kind of a hand tool to an IRA creates immense opportunities and unique ways of exploring
material properties and conditions. In that manner, architects have attached; pens, heat guns, extruders,
grippers, hot-wire cutters, grinders, drills, chisels, suction heads, welders, etc… as end effectors to the
IRAs.
When dealing with custom EEs, the main concerns are to be aware of the tool centre point (TCP) that is the
gravitational centre and the payload of the proposed EE. The EEs can be modelled in a 3D modelling software
with the tool base at 0, 0, 0 point, where most software use as an import point for the simulation of the
kinematics model of the IRA. The weight and the location of the EE effects the movement of the IRA by means
of vibration and locating the workspace and the material that is worked on.
Therefore, they should be calibrated in relation to these parameters. Calibration of an IRA is important to
achieve precision and accuracy in the outcomes of the manufactured models. Calibrations are done through
3Points Calibration (XYZ) method or 4-point calibration method.
Sensors
Sensors are the receptors of the IRA. Sensors are used:
- to contextualize a robot within an environment (Gramazio, Kohler),
- to use the IRAs in their full capacity,
- to sense the different material qualities,
- to create engagement possibilities with the materials,
- to allow safe human-robot collaboration.
Touch sensors, vision scanners, microphones, force control sensors, motion tracking systems are used to gather information from IRAs surroundings and materials. The gathered information through the sensors are fed into the robot control systems to create feedback loops to allow real-time manipulation of the IRAs movements. Such feedback loops are necessary to have greater control over the IRA as well as getting accurate or desirable outcomes.
Tracks, Turntables and Work Bases
Most of the IRAs used in architectural manufacturing are 6-axis. In some cases, where more than 6 axis is necessary, the IRA is set up on a moving track, or the worktable is a turntable. This provides flexibility in the movement of the IRA. In case of the IRA used as a tool in a construction field, it can be mobile allowing autonomous vehicle properties to be applied. By scanning its surroundings, the IRA can adjust its movements in relation to obstacles, as well as follow directives to complete predefined spatial tasks.
The Future of Manufacturing
With support from the Innovative Manufacturing Cooperative Research Centre (IMCRC), Design Robotics is collaborating to present a range of new
fabrication and vision systems solutions. The goal is simple – to design for human intelligence and optimize
the relationship between people and machines.
Pushing the limits of industrial robotics is a move to empower people. Navigating the increasing complexity
of manufacturing inevitably supports human experience and enhances skills acquisition. At its heart, this
approach celebrates the best of what robots and machines can achieve – problem-solving, and the best of what
humans can do – social intelligence and contextual understanding.